


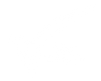
Guide to TIG Welding
What is the TIG welding process?
A number of terms are used for the process such as:
TIG Tungsten Inert Gas
GTAW Gas Tungsten Arc Welding
The idea of welding in an inert gas atmosphere was developed in 1890, but even in the early 1900’s, welding non-ferrous materials like aluminum and magnesium remained difficult because these metals reacted rapidly with the air, resulting in porous and dross filled welds. In the early 1930’s to solve the problem, bottled inert gases were used. A few years later, a direct gas-shielded welding process emerged in the aircraft industry for welding magnesium.
This TIG process was perfected in 1941 and became known as heliarc or tungsten inert gas welding because it utilised a tungsten electrode and helium as a shielding gas.
Finally, the development of alternating current units made it possible to stabilise the arc and produce high quality aluminum and magnesium welds.
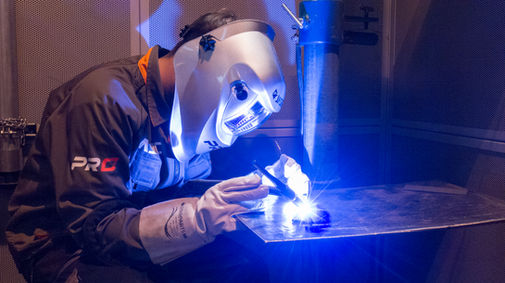
TIG Welding Process Description
The TIG welding process consists of an electric arc to provide heat created between a non consumable electrode and the work piece to be welded. The molten pool created by this arc is shielded by a gas which is used to exclude the surrounding atmosphere from the weld area. The most common gases used are inert such as helium or argon as they have no reaction with the weld pool and being transparent provide the welder with good visibility of the TIG arc. Sometimes a reactive gas can be added such as hydrogen which can increase the heat of the arc and speed of welding.
The TIG process produces very high temperatures of up to 19000°C. The TIG arc only produces a source of heat and if additional material is required to complete a weld then this is added either manually or automatically in the form of a consumable filler wire.
When first developed the TIG process used helium gas as shield gas and was often referred to as the Heliarc process.
How The TIG Welding Process Works
The process works by creating a high temperature arc between the electrode and work piece within a gas shielded area. This then creates a molten pool which is used to either fuse the material to be welded without the addition of any filler material (an autogenous weld) or filler material can be added. The process can be used in either direct current (DC) or alternating current (AC) modes.
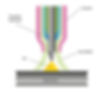
The concentrated arc of the TIG process allows precise control of the heat input and thus enables a narrow heat affected zone. This concentrated arc and heat input makes the process well suited to welding materials with high heat conductivity such as aluminium.
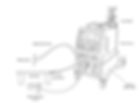
The Jasic TIG Welding System
TIG Inverter Power Source
The TIG welding inverter power source can be either single or three phase input and have either DC or AC/DC output (AC only output machines are now rare in the marketplace).
DC TIG welding inverters are used in the welding of materials such as stainless steel, steel, copper etc whereas the AC welding inverters are used to weld materials such as aluminium which have a refractory oxide coating.
The TIG power source will generally have an output open circuit voltage of between 60 and 90V but always check with the manufacturer’s data. The TIG power source will provide a constant current type output and the current varies little with arc length changes although the longer the TIG arc is, the wider it becomes and is harder to control. The TIG welding inverter will normally contain all the process controls, power supply unit, arc starting unit, gas valves and optional controls for additional cooling.
Power sources can vary from simple electro mechanical types to sophisticated micro computer controlled inverters and many offer an MMA welding function in addition to the TIG function.
Welding Gas Cylinder
The welding gas cylinder contains gas stored under pressure usually 230 or 300 Bar and should be handled carefully. This gas shields the weld area from contaminants and enhances the TIG welding process.
The Regulator/Flow Meter
This regulates the cylinder pressure to a usable shielding gas pressure and controls the flow of gas. Regulators are usually a fixed outlet pressure and an independent flow meter is used for flow control. They are normally a single stage configuration and have a single gauge.

TIG Torch, Regulator and Work Return

Jasic Foot Control Unit
Remote Controls
In certain application it may not be possible for the operator to access the machine controls from the welding area.
The operator may need to control various parameters locally such as current, slope control etc. The majority of welding inverters designed for TIG welding provide remote control capability.
The remote control offers usually current control as a minimum. In addition many remote systems can almost duplicate all the major parameters.
The remote controls come in several variants, i.e. hand held, torch mounted, bench mounted and most commonly a foot control unit.
Under Gear / Inverter Trolley
When using the TIG welding inverter it is always best practice to keep the TIG torch length as short as possible. Therefore to have the TIG welding inverter mobile is a definite advantage. Many TIG welders are fitted with or have optional under gear kits that transport the welding inverter and ancillaries along with the gas cylinder easily.


TIG Welding Torch
The TIG welding torch is a critical part of the TIG process. It is the point at which the arc is created and whilst the majority of heat goes into the arc the TIG welding torch is subjected to high heat levels.
As the torch is held by the operator it must remain cool whilst still being easily manoeuvrable and compact in size.
This heat is removed from the torch by either air/gas cooling or water cooling.
Where torches are required for high production or use high amperage then these would normally be water cooled and where lower amperage or lighter duty is required these would normally be air cooled.

Jasic Air-Cooled TIG Torch

Jasic Water-Cooled TIG Torch
Air/Gas cooled TIG torches require no additional cooling other than the surrounding air and gas flow.
Higher current air cooled torches are often larger and less flexible to use than water-cooled torches.
The cable carrying the welding current must be heavier than the cable in water-cooled torches.
Water-cooled TIG torches are designed so that water is circulated through the torch cooling it and the power cable. The power cable is contained inside a hose and the water returning from the torch flows around the
power cable providing the necessary cooling. This method of cooling means the power cable can be relatively small, making the entire cable assembly light and easily manipulated. Care must be taken when using a water cooled torch that a lack of coolant or no coolant at all will cause the polyethylene or braided rubber sheath to
melt or possibly the power cable will melt. Always check the flow rate required to cool the TIG torch.
TIG Welding Torch Components

TIG Torch Body / Head
The torch body is usually covered by a rigid phenolic material or a rubberised covering. They can be rigid or flexible variants, with or without valves.
Collet Body
The TIG collet body screws into the torch body. It is replaceable and is changed to accommodate different size tungsten electrodes and their respective collets.

Collet

The tungsten welding electrode is held in the TIG welding torch by the collet. The collet is usually made of copper or a copper alloy. The collet’s grip on the electrode is secured when the torch back cap is tightened in place. Good electrical contact between the collet and tungsten electrode is essential for good current transfer.
Gas Lens Body
A gas lens is a device that can be used in place of the normal collet body. It screws into the torch body and is used to reduce turbulence in the flow of shield gas and produce a stiff column of undisturbed flow of shielding gas. A gas lens will allow the welder to move the nozzle further away from the joint allowing increased visibility of the arc.
A much larger diameter nozzle can be used which will produce a large blanket of shielding gas.
This can be very useful in welding material like titanium. The gas lens will also enable the welder to reach joints with limited access such as inside corners.
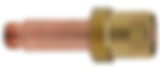
Ceramic Cup

Gas cups are made of various types of heat resistant materials in different shapes, diameters and lengths. The cups are either screwed onto the collet body or gas lens body or in some cases pushed in place. Cups can be made of ceramic, metal, metal-jacketed ceramic, glass or other materials. Ceramic is the most popular but can be easily broken.
TIG Tungsten Welding Electrodes

TIG welding electrodes are a ‘non consumable’ as it is not melted into the weld pool and great care should be taken not to let the electrode contact the welding pool to avoid weld contamination. This would be referred to as tungsten inclusion and may result in weld failure. Electrodes will often contain small quantities of metallic oxides which can offer the following benefits:
• Assist in arc starting
• Improve current carrying capacity of the electrode • Reduce the risk of weld contamination
• Increase electrode life
• Increase arc stability
Oxides used are primarily zirconium, thorium, lanthanum or cerium. These are added usually 1% - 4%.
Types of Tungsten Welding Electrodes
Pure Tungsten (Green) AWS A5.12 EWP, ISO 6848 WP
These TIG electrodes are unalloyed, ‘pure’ tungsten with a 99.5% tungsten minimum and are relatively low cost. They provide good arc stability when using AC current, with either balanced wave or unbalanced wave and continuous high-frequency stabilization. Pure tungsten electrodes are preferred for AC sine wave welding of aluminium and magnesium because they provide good arc stability with both argon and helium shielding gas.
The pure tungsten electrode easily forms a balled end but has a tendency to spit at higher currents and this should be considered when making critical welds.
Ceriated 2% (Grey) AWS A5.12 EWCe-2, ISO 6848 WC20
These TIG electrodes are alloyed with about 2% ceria, a non-radioactive material and the most abundant
of the rare earth elements. The addition of this small percentage of cerium oxide increases the electron emission qualities of the electrode which gives them a better starting characteristic and a higher current carrying capacity with no spitting. These are all-purpose electrodes that will operate successfully with AC or DC electrode negative. Compared with pure tungsten, the ceriated tungsten electrodes provide for greater arc stability. They have excellent arc starting properties at low current. If used on higher current applications the cerium oxide may be concentrated to the excessively hot tip of the electrode. This condition and oxide change will remove the benefits of the cerium. The non radioactive cerium oxide has slightly different electrical properties as compared to the thoriated tungsten electrodes.
The cerium electrodes work well with the Advanced Squarewave power sources and should be ground to a modified point.
Lanthanated (1% Lanthanum, Black), (1.5% Lanthanum, Gold),
(2% Lanthanum, Blue) AWS A5.12 EWLa-, ISO 6848 WL
These TIG electrodes are alloyed with non radioactive lanthanum oxide, often referred to as lanthana, another of the rare earth elements. These electrodes have excellent arc starting, low erosion rate, arc stability and excellent re-ignition characteristics.
The addition of 1 – 2% lanthana increases the maximum current carrying capacity by approximately 50% for a given size electrode using alternating current compared to pure tungsten. The higher the percentage of lanthana, the more expensive the electrode. Since lanthana electrodes can operate at slightly different arc voltages than thoriated or ceriated tungsten electrodes these slight changes may require welding parameters and procedures to be adjusted. The 1.5% content appears to most closely match the conductivity properties of 2% thoriated tungsten. Compared to cerium and thorium the lanthana electrodes had less tip wear at given current levels. Lanthanum electrodes generally have longer life and provide greater resistance to tungsten contamination of the weld.
The lanthana is dispersed evenly throughout the entire length of the electrode and it maintains
a sharpened point well, which is an advantage for welding steel and stainless steel on DC or the AC from Advanced Squarewave power sources. Thus the lanthana electrodes work well on AC or DC electrode negative with a pointed end or they can be balled for use with AC sine wave power sources.
Thoriated (2% Thorium, Red) AWS A5.12 EWTh-2, ISO 6848 WT20
Thoriated electrodes both 1 and 2% are very commonly used electrodes since they were the first to show better arc performance over pure tungsten for DC TIG welding.
However, thoria is a low-level radioactive material, thus vapours, grinding dust and disposal of thorium raises health, safety and environmental concerns. The relatively small amount present has not been found to represent a health hazard. But if welding will be done in confined spaces for prolonged periods of time, or if electrode grinding dust might be ingested, special precautions should be taken concerning proper ventilation. The welder should consult informed safety personnel and take the appropriate
steps to avoid the thoria. The thoriated electrode does not ball as does the pure tungsten, cerium or lanthana electrodes. Instead, it forms several small projections across the face of the electrode when used on alternating current. When used on AC sine wave machines, the arc wanders between the multiple projections and is often undesirable for proper welding. Should it be absolutely necessary to weld with these type machines, the higher content lanthana or thoria electrodes should be used. The thoriated electrodes work well with the Advanced Squarewave power sources and should be ground
to a modified point. These electrodes are usually preferred for direct current applications. In many DC applications, the electrode is ground to a taper or pointed. The thorium electrode will retain the desired shape in those applications where the pure tungsten would melt back and form the ball end. The thoria content in the electrode is responsible for increasing the life of this type over the pure tungsten.
Zirconiated (1% Zirconium, White) AWS A5.12 NONE, ISO 6848 WZ8
This TIG tungsten is alloyed with zirconium oxide (zirconia) and is preferred for AC TIG welding when the highest quality work is necessary and where even the smallest amounts of weld pool contamination cannot be tolerated. This is accomplished because the zirconium alloyed tungsten produces an extremely stable arc which resists tungsten spitting in the arc. The current carrying capability is equal to or slightly greater than an equal sized cerium, lanthana or thorium alloyed electrode. Zirconium electrodes are typically used only for AC welding with a balled end.
The tungsten electrodes come in a variety of diameters and you would select the appropriate diameter for the current to be used and type for the process mode. To physically identify the tungsten type the end is dipped with a colour. Take care to grind the non coloured end for welding.
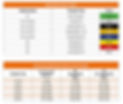
Tungsten Preparation
TIG DC Welding
& TIG AC Welding with Some Modern Inverter Controlled Welders)
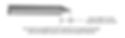
When welding at low current the electrode can be ground to a point. At higher current a small flat on the end of the electrode is preferable as this helps with arc stability.
TIG AC Welding
(Standard AC Welding Inverters and Sinusoidal Operations)
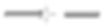
TIG Tungsten Electrode Grinding
It is important when grinding the welding electrode to take all necessary precautions such as wearing eye protection and ensuring adequate protection against breathing in any grinding dust.
TIG Tungsten electrodes should always be ground lengthwise and not in a radial operation. Electrodes ground in a radial operation tend to contribute to arc wander due to the arc transfer from the grinding pattern. Always use a grinder solely for grinding electrodes to avoid contamination

TIG Welding Filler Wire
Filler wires come in many different material types and usually as cut lengths, unless some automated feeding is required where it will be in reel form. Always consult the manufacturer’s data and welding requirements.
TIG Welding Gases
Gases normally used in the TIG welding process are:
Argon Gas
Argon is obtained as a by product in the manufacturing of oxygen. Argon may be obtained in the gaseous state in cylinders or as a liquid in specially constructed cylinders or in bulk tanks.
When choosing a shielding gas, a fact that must be considered is the ionization potential of the gas. Ionization potential is measured in volts and is the point where the welding arc will be established between the electrode and the work piece through the shielding gas. In other words, it is the voltage necessary to electrically charge the gas so that it will conduct electricity.
The ionization potential of argon is 15.7 volts. So this is the minimum voltage that must be maintained in the welding circuit to establish the arc or to weld with argon. The ionization potential is different for every gas and has a major effect on the arc and weld bead. The ionization potential for helium is 24.5 volts. Comparing two welding circuits, each being equal except for shielding gas, the arc voltage produced with argon would be lower than that produced by helium. Argon has low thermal conductivity which means it is not a good conductor of heat. This results in a more compact, higher density arc. Arc density refers to the concentration of energy in the arc. With argon this energy is confined to a narrow or more ‘pinpointed’ area. Argon provides excellent arc stability and cleaning action even at low amperages.
Helium
Unlike argon, helium has high thermal conductivity. Due to this higher thermal conductivity, the arc column expands, reducing current density in the arc. The arc column will become wider and more flared out than the arc column with argon shielding gas. The more flared out the arc column, the more work surface area is being heated. The heat at the centre of the arc can move more readily downward towards the colder metal at the bottom of the work piece. This results in a deeper penetrating arc. It was mentioned previously that with an equivalent arc length, helium will produce a higher arc voltage than will argon. Since the total power is a product of voltage and amperage, it is apparent that more heat energy is available with helium.
Helium or argon-helium mixtures are desirable on thick material and where high travel speeds are desired. The use of 2:1 helium to argon gas mixture has also been shown to yield lower porosity welds in production situations by allowing wider variation in welding parameters.
With helium shielding any slight variation of arc length can have quite an affect on arc voltage and consequently total arc power. For this reason, helium is not as desirable as argon for manual welding applications.
Because of its higher ionization potential, it is more difficult to start an arc with helium shielding gas, especially at lower amperages.
Argon is used almost exclusively when welding at 150 amps and lower. As helium is a light gas, flow rates are usually two or three times higher than argon for equivalent shielding. The cost of helium is considerably more than argon and with the increased flow rate, total cost of shielding goes up sharply. The cost must be weighed against increased penetration on thick material and the increased travel speed attainable.
Hydrogen
Just as helium is mixed with argon to take advantage of the best features of both gases, hydrogen is mixed with argon to further constrict the arc and produce a cleaner weld with a greater depth to width ratio (penetration). This mix is used primarily for welding austenitic stainless steel and some nickel alloys. The addition of hydrogen to argon also increases travel speed. It should be noted that an argon hydrogen mix will introduce the risk of hydrogen cracking and metal porosity particularly in multi pass welds.
Nitrogen
Nitrogen when mixed with argon provides the capability of producing more energy to the work than with argon alone. This can be particularly beneficial when welding materials of high conductivity such as copper. However, a nitrogen mix cannot be used on ferrous metals such as steel and stainless steel because nitrogen pick up in the weld pool causes a significant reduction in strength and a weaker, more porous bead.
Gas Flow Rates
The correct flow rate is an adequate amount to shield the molten weld pool and protect the tungsten electrode. More than this amount is wasted. The correct flow rate in litres per min (or cubic feet per hour) is influenced by many variables that must be considered on each application. Generally speaking, when the welding current, cup diameter or electrode stick out is increased, the flow rate should be increased.
When welding in the AC mode the current reversals have a disturbing affect on the shielding gas and flow should be increased by 25% and of course, when welding in a draft situation, flow rate should be doubled.
When welding in difficult areas excessive flow rates can cause turbulence and air entrapment. In this situation, the effectiveness of the shielding gas can be improved by reducing the gas flow by about 25%.
As a guide the flow rate is normally around 8-12 l/m for argon but can be double that for helium.
TIG Welding Inverter Controls

Current Control
This control is normally a stepless adjustment of the welding current. This can either be via the front panel of the
welding inverter, via a remote control foot or hand operated control or a combination of both.
Welding Mode Selection
This selects the welding modes. These can be: MMA TIG AC mode DC mode Pulse welding
AC Frequency
The normal mains frequency of equipment is 50Hz. However, modern TIG welding inverters are able to vary this frequency for example 50-100Hz. Many welders will often settle on around 70Hz.
Balance Control
This selects the percentage of cleaning between positive and negative cycles in the AC welding mode. Balance zero is normally 50:50 positive and negative. More cleaning is more positive and less negative and more penetration is the opposite i.e. more negative and less positive. Controls will often show a zero as the balanced state and a +10 -10 indicator range either side of zero.
With the correct setting of the frequency and balance controls it is possible to use a smaller size tungsten.
Pulse Control
Pulse control is a variation of control of the welding current. The control often consists of a peak welding and background welding current level and also the times of each level. In addition there may be a frequency control. On some welding inverters pulsing may be preset ratios and just high and low frequency selections offered.

Slope Control
The slope control is a time control by which the rise or fall of current from welding level can be set.
Gas Flow Timers
Timers that are used to control the time that shield gas is fed to shield the weld area.
Gas flow prior to an arc being struck (pre gas or pre flow) is used to purge the weld zone and the welding torch of any contaminant. It would normally be used when the material to be welded is sensitive to atmospheric contamination.
This time setting will have to complete its cycle prior to any other functions starting.
Following the completion of the weld and the weld zone is cooling, a timer controls the time gas flows (post gas or post flow) without any other machine functions in operation to shield the weld zone.
In addition, post gas flow protects the cooling tungsten electrode from contamination.