


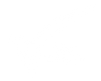

MIG Inverter Welders
click text to select a welding inverter
Jasic offer an expansive range of 15 - IGBT MIG/MAG inverter welders from UK stock for immediate delivery. Ranging from a single-phase 160 amp compact, to a three-phase 450 amp separate 'water-cooled' welding inverter. Some key features found within our range of MIG welding machines include: Digital Meters, Synergic, Memory Storage, Pulse, Double Pulse, Auto-Diagnostics, 4 Roll-Drive, Water-Cooling etc.
All our MIG welding inverters fully comply with all quality/safety standards, and come with a comprehensive 5 year warranty, supported by a highly skilled team of Jasic Technicians.
If you need any help selecting a Jasic MIG welding inverter for your application, please see our Purchasing Assistance Guide or Jasic MIG Selection Guide Chart
Furthermore, If you would like a 'hands on' MIG inverter demonstration before you decide, please contact us.
Compact MIG Inverters
MIG/MMA - 160A@35% - 230V
MIG/MMA - 200A@35% - 230V

MIG/MMA - 200A@35% - 95V/265V - PFC Energy Saving
MIG/MMA - 200A@35% - 230V - Synergic Control - Digital Meters
MIG/MMA - 250A@35% - 230V - Digital Meters -Spool Gun Option
MIG/MMA - 250A@40% - 230V - Digital Meters -Spool Gun Option
MIG/MMA/Lift-Arc - 350A@40% - 415V - Digital Meters -Spool Gun Option
Separate MIG Inverters
MIG/MMA - 270A@30% - 230V - Digital Meters - Single Phase
MIG/MMA -350A@40% -415V - Digital Meters - 4-Roll Feed
MIG/MMA -400A@100% -415V - Digital Meters - 4-Roll Feed
MIG 450S Inverter Welder
Water-Cooled
MIG/MMA -400A@100% -415V - Digital Meters - 4-Roll Feed - Water-Cooled
MIG 350P Pulse Synergic Inverter Welder
Water-Cooled
MIG/MMA -350A@60% -415V - Synergic- Pulse - Digital Meters - 4-Roll Feed - Water-Cooled
MIG 500S Synergic Inverter Welder
Water-Cooled
MIG/MAG -400A@100% -415V - Synergic -Digital Meters- 4-Roll Feed - Water-Cooled
MIG 500P Pulse Synergic Inverter Welder
Water-Cooled
MIG/MAG -500A@50% -415V - Pulse - Synergic -Digital Meters- 4-Roll Feed - Water-Cooled
Use the Jasic MIG Selection Guide
to help find the right MIG model
MIG Welding Process
The MIG welding process was developed to meet the production demands of the war and post war time economies. This welding process utilises an electric arc power source, continuously fed consumable MIG wire shielded by gas.
A number of terms are used for the process such as:
MIG – Metal inert gas welding
MAG – Metal active gas welding
GMAW – Gas metal arc welding
Selecting a good MIG welding equipment will make all the difference when it comes to MIG welding.
The wrong type or poor quality equipment can cause frustration, poor weld quality and waste a lot of time.
Whilst a wide range of MIG welding equipment is available the development of new inverter technologies have made equipment easier to use and set up often by automating many features allowing the welder to concentrate on
welding technique.
The MIG welding process was first patented for the welding of aluminium in 1949 in the USA.
The process uses the heat that is generated by an electric arc formed between a bare consumable wire electrode
and the work piece. This arc is shielded by a gas to prevent oxidation of the weld.
In the MIG process an inert shielding gas is used to protect the electrode and weld pool from contamination and enhance the arc. Originally this gas was helium.
In the early 1950’s the process became popular in the UK for welding aluminium using argon as the shielding gas.
Development in the use of different gases resulted in the MAG process. This is where other gases were used, for example carbon dioxide and sometimes users refer to the process as CO2 welding. Gases such as oxygen and carbon dioxide were added and are active constituents to the inert gas to improve the welding performance.
Although the MAG process is in common use today it is still referred to as MIG welding although technically this is not correct. The process began to prove itself as an alternative to stick electrode (MMA) and TIG (GTAW) offering high productivity and deposition rates. The process also helps reduce any weld defects from the increased stop/starts used in MMA. However, the welder must have a good knowledge of the system set up and maintenance to achieve satisfactory MIG welds.
MIG Welding Process
'Free product training at the Jasic academy when you purchase any MIG inverter'
