


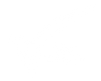

Plasma Cutters
click to select a plasma cutter
Jasic offers a high quality range of Plasma Cutters from UK stock for immediate delivery. Ranging from a single-phase 45 amp, to a three-phase 160 amp cutting inverter that cuts up to 50mm. Some key features found within our range of plasma cutters include: Power Factor Correction (Cut 45), All IGBT Inverters, Generator Friendly (Requires regulated output), Digital Meter.
All our plasma cutters fully comply with all quality/safety standards, and come with a comprehensive 5 year warranty, supported by a highly skilled team of Jasic Technicians.
Furthermore, If you would like a 'hands on' plasma cutter demonstration before you decide, please contact us.
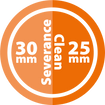
The single-phase Cut 45 PFC plasma cutter produces a genuine 15mm clean cut and a 20mm severance cut
The three-phase Cut 60 plasma cutter produces a genuine 20mm clean cut and a 25mm severance cut
The three-phase Cut 80 plasma cutter produces a genuine 25mm clean cut and a 30mm severance cut
The three-phase Cut 100 plasma cutter produces a genuine 30mm clean cut and a 35mm severance cut
The three-phase Cut 160 plasma cutter produces a genuine 45mm clean cut and a 50mm severance cut
Plasma Cutting Basics

The plasma arc cutting process basics can be seen in the illustration.The basic principle is that the plasma arc is formed between the electrode and the work piece through a constricting fine bore copper nozzle. This will increase the speed and temperature of the plasma exiting the tip. The temperature of the plasma is in excess of 15000°C and the speed can approach that of sound.
This plasma gas flow in conjunction with the high temperature enables a deeply penetrating plasma jet to cut through the work piece material and at the same time molten material is blown away from the cut.
Air Plasma Cutting
Air plasma cutting is one of the most common variations used today. It was first introduced in the early 1960's for cutting mild steel. The oxygen present in the air provided additional energy from the exothermic reaction with molten steel.
Compared to plasma cutting with nitrogen this additional energy increased cutting speeds by about 25%.

What makes up the Plasma Cutting System?
The Plasma cutting process is an effective means of cutting both thin and thick materials. Hand-held torches can usually cut up to around 50mm thick steel plate, whilst larger automated water cooled machine mounted torches can cut steel up to 150mm often used with a mechanised computer controlled system.
Formerly, plasma cutters could only work on conductive materials; however, new technologies allow the plasma ignition arc to be enclosed within the nozzle, thus allowing the cutter to be used for non-conductive work pieces such as glass and plastics (special conditions apply).
For the purposes of this guide we will only deal with the plasma cutting of metals.
Plasma Cutter Power Source
The plasma cutter power source required for the plasma arc process is a DC output and must have
a drooping characteristic and a high voltage.The operating voltage needed to maintain the plasma arc is typically 90 to 130 VDC, but the open circuit voltage neededto initiate the arc can be as high as 330V DC.
Plasma Cutters come in a variety of formats from transformer rectifier to inverter type.
Inverters are particularly suited to applications which require precise control or portability.

When the process is started, what is called a pilot arc is formed within the torch body between the electrode and the cutting tip. To start cutting, the arc must be transferred to the work piece from the nozzle in what is referred to as ‘transferred’ arc mode.
The electrode has a negative polarity and the work piece a positive polarity so that the majority of the arc energy (approximately two thirds) is used for cutting.
Compressed Air
Can be used on all materials. Compressed air is easily accessible and produces relatively fast cuts with good cutting appearance on most materials especially carbon steel. Air is comprised of 20% oxygen and 80% nitrogen (approximately).
The oxygen provides an exothermic reaction with easily oxidized materials such as carbon steel which reduces dross and increases cutting speed. Unfortunately the nitrogen content in air produces a nitriding effect on steel that provides a very hardened surface and the nitride finish can create weld porosity if the raw cut surface is directly welded.
When cutting stainless steels with air expect a brown discoloured cut edge this is an oxide layer from the oxygen and this layer can affect some welding processes.
Plasma Cutting Torch
A very important part of the plasma cutting system is the torch. They come in all shapes and sizes both gas and liquid cooled. They can operate with air or in some cases mixed gases. Older type torches tended to be large and heavy but manufacturers have over the years engineered models which are smaller and lighter than the older types but often with a higher capacity. Torches may have an electrical or mechanical pilot arc system as previously described.

