MMA (Stick) Welding Electrode Guide
- Jasper Jasic
- Nov 6, 2018
- 5 min read
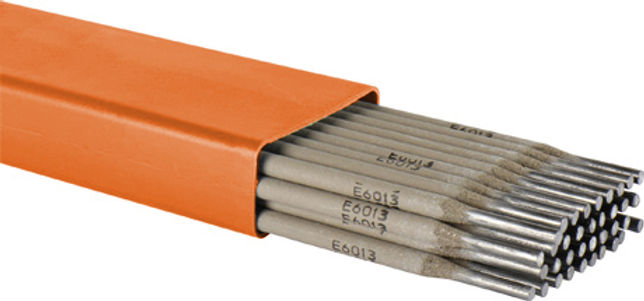
Types of Flux/Electrodes
The stability of the arc, depth of penetration, metal deposition rate and positional features are significantly influenced by the chemical composition of the flux coating on the electrode. Electrodes can be divided into three main types:
• Basic • Cellulosic
• Rutile
Basic Welding Electrodes
Basic welding electrodes contain a high proportion of calcium carbonate (limestone) and calcium fluoride (fluorspar) in the coating. This makes their slag coating more fluid than rutile coatings - this is also fast-freezing which assists welding in the vertical and overhead position. These electrodes are used for welding medium and heavy section fabrications where higher weld quality, good mechanical properties and resistance to cracking (due to high restraint) are required.
Features:
Low hydrogen weld metal
Requires high welding currents/speeds
Poor bead profile (convex and coarse surface profile)
Slag removal difficult
When these electrodes are exposed to air moisture pick-up is rapid. Because of the need for hydrogen control these electrodes should be thoroughly dried in a controlled temperature drying oven. Typical drying time is one hour at a temperature of approximately 150oC to 300oC but you should always consult the manufacturer data before use.
After controlled drying, basic and basic/rutile electrodes must be held at a temperature between 100oC and 150oC to help protect them from re-absorbing moisture into the coating. These conditions can be obtained by transferring the electrodes from the main drying oven to a holding oven or a heated quiver at the workplace.
Metal Powder Electrodes
Metal powder electrodes contain an addition of metal powder to the flux coating to increase the maximum permissible welding current level. Thus, for a given electrode size, the metal deposition rate and efficiency (percentage of the metal deposited) are increased compared with an electrode containing no iron powder in the coating.
The slag is normally easily removed. Iron powder electrodes are mainly used in the flat and H/V positions to take advantage of the higher deposition rates. Efficiencies as high as 130-140% can be achieved for rutile and basic electrodes without marked deterioration of the arcing characteristics but the arc tends to be less forceful which reduces bead penetration.
NOTE: The quality of weld relies upon consistent performance of the electrode. The flux coating should not be chipped, cracked or more importantly, allowed to become damp. Electrodes are made with different types of coating and require different handling.
Cellulosic Welding Electrodes
Cellulosic welding electrodes contain a high proportion of cellulose in the coating and are characterised by a deeply penetrating arc and a rapid burn-off rate giving high welding speeds. Weld deposit can be coarse and with fluid slag, de slagging can be difficult. These electrodes are easy to use in any position and are noted for their use in the ‘stovepipe’ welding technique.
Features:
• Deep penetration in all positions • Suitability for vertical down welding • Reasonably good mechanical properties • High level of hydrogen generated - risk of cracking in the heat affected zone (HAZ)
These electrode coatings are designed to operate with a definite amount of moisture in the coating. The coating is less sensitive to moisture pick-up and does not generally require a drying operation. However, drying may be necessary in cases where ambient relative humidity in which the electrodes have been stored in, has been very high.
Rutile Welding Electrodes
Rutile welding electrodes contain a high proportion of titanium oxide (rutile) in the coating. Titanium oxide promotes easy arc ignition, smooth arc operation and low spatter. These electrodes are general purpose electrodes with good welding properties. They can be used with AC and DC power sources and in all positions. The electrodes are especially suitable for welding fillet joints in the horizontal/vertical (H/V) position.
Features:
• Moderate weld metal mechanical properties • Good bead profile produced through the viscous slag • Positional welding possible with a fluid slag (containing fluoride)
• Easily removable slag
The rutile coatings can tolerate a limited amount of moisture and coatings may deteriorate if they are over dried. Always consult the manufacturer data before use.
Hard Wear/Facing Welding Electrodes
Hard facing or wear electrodes are used primarily to put a hard surface over a softer base material. There is an extensive range of these types of products and a common use area is the repair of wearing surfaces such as teeth on earth moving and mining equipment.
DC Copper Coated Welding Electrodes
This is the most common type because of its comparatively long electrode life. These electrodes are constructed by mixing and baking carbon, graphite and a binding agent and coating them with copper. They provide stable arc characteristics and uniform grooves.
DC Plain Electrodes
These are constructed in the same way as the DC copper coated electrode but without the copper coating. They are more rapidly consumed compared to copper coated in use
AC Coated Electrodes
These electrodes are constructed by mixing and baking carbon, graphite and a special binding agent with added rare earth materials to help with arc stabilization. They are copper coated. The process uses compressed air at between 80-100 psi at the electrode holder.
Increasing air pressure will not remove metal more efficiently.
Welding Electrode Storage
Electrodes should always be kept in a dry and well-ventilated store. It is good practice to stack packets of electrodes on wooden pallets or racks well clear of the floor. Also, all unused electrodes which are to be returned should be stored so they are not exposed to damp conditions to regain moisture.
Good storage conditions are 10°C above external air temperature. As the storage conditions are to prevent moisture from condensing on the electrodes, the electrode stores should be dry.
Under these conditions and in original packaging, electrode storage time is practically unlimited. Modern electrodes are now available in hermetically sealed packs which remove the need for drying. However, if necessary, any unused electrodes must be redried according to manufacturer’s instructions.
Drying of Electrodes
Drying is usually carried out in accordance with the manufacturer’s recommendations and requirements will be determined by the type of electrode.
Many electrodes are now available in hermetically sealed containers. These vacuum packs obviate the need for drying the electrodes immediately prior to use. If however the container has been opened or damaged, it is essential that the electrodes are re dried according to the manufacturer’s instructions.
Electrode Selection
The electrode diameter selection is based on the work piece thickness, welding position, joint form, welding layer etc.
Welding current level is determined by the size of electrode - the normal operating range and current are recommended by manufacturers. Typical operating ranges for a selection of welding electrode sizes are illustrated in the table.

Electrodes should be dry and used according to the instructions. This will reduce the hydrogen in the molten pool and welding seam, avoiding the blowholes and cold cracking.
In the welding process, the arc must not be too long; otherwise, it will cause unstable arc burning, large amounts of spatter, light penetration, undercut, blowholes etc. If the arc is too short, it will cause electrode sticking to the work piece.
In MMA welding the arc length is usually equal to 0.5~1.0 times the diameter of the electrode. The basic electrode’s arc length is not more than the electrode diameter and short arc welding is preferred. When using acid electrodes the arc length is equal to the electrode diameter.
Comments