Welding Safety Guide
- Jasper Jasic
- Nov 12, 2018
- 5 min read

Fumes and welding gases
Locate the equipment in a well-ventilated position. Keep your head out of the fumes. Do not breathe the fumes. Ensure the welding zone is in a well-ventilated area.
If this is not possible provision should be made for suitable fume extraction.
If ventilation is poor, wear an approved respirator. Read and understand the Material Safety Data Sheets (MSDS’s) and the manufacturer’s instructions for metals, consumable, coatings, cleaners and de-greasers. Do not weld in locations near any de-greasing, cleaning or spraying operations. Be aware that heat and rays of the arc can react with vapours to form highly toxic and irritating gases.

Precautions against fire and explosion
Avoid causing fires due to sparks and hot waste or molten metal.
Ensure that appropriate fire safety devices are available near the cutting/welding area. Remove all flammable and combustible materials from the cutting/welding zone and surrounding areas.
Do not cut/weld fuel and lubricant containers, even if empty. These must be carefully cleaned before they can be cut/welded. Always allow the cut/welded material to cool before touching it or placing it in contact with combustible or flammable material.
Do not work in atmospheres with high concentrations of combustible fumes, flammable gases and dust.
Always check the work area half an hour after cutting to make sure that no fires have begun.
Take care to avoid accidental contact of electrode to metal objects. This could cause arcs, explosion, overheating or fire.
General operating safety
Never carry the equipment or suspend it by the carrying strap or handles during welding.
Never pull or lift the machine by the welding torch or other cables. Always use the correct lift points or handles. Always use the transport under gear as recommended by the manufacturer. Never lift a machine with the gas cylinder mounted on it.
If the operating environment is classified as dangerous, only use S-marked welding equipment with a safe idle voltage level. Such environments may be for example: humid, hot or restricted accessibility spaces.
Working environment
Ensure the machine is mounted in a safe and stable position allowing for cooling air circulation.
Do not operate equipment in an environment outside the laid down operating parameters. The welding power source is not suitable for use in rain or snow.
Always store the machine in a clean, dry space.
Ensure the equipment is kept clean from dust build up. Always use the machine in an upright position.
Protection from moving parts
When the machine is in operation keep away from moving parts such as motors and fans. Moving parts, such as the fan, may cut fingers and hands and snag garments.
Protections and coverings may be removed for maintenance and controls only by qualified personnel after first disconnecting the power supply cable.
Replace the coverings and protections and close all doors when the intervention is finished and before starting the equipment.
Take care to avoid getting fingers trapped when loading and feeding wire during set up and operation. When feeding wire be careful to avoid pointing it at other people or towards your body.
Always ensure machine covers and protective devices are in operation.

Risks due to magnetic fields
The magnetic fields created by high currents may affect the operation of pacemakers or electronically controlled medical equipment.
Wearers of vital electronic equipment should consult their physician before beginning any arc welding, cutting, gouging or spot welding operations.
Do not go near welding equipment with any sensitive electronic equipment as the magnetic fields may cause damage.
Keep the torch cable and work return cable as close to each other as possible throughout their length. This can help minimise your exposure to harmful magnetic fields.
Do not wrap the cables around the body.

Handling of compressed gas cylinders and regulators
Always check the gas cylinder is the correct type for the welding to be carried out.
All cylinders and pressure regulators used in welding operations should be handled with care. Never allow the electrode, electrode holder or any other electrically “hot” parts to touch a cylinder. Keep your head and face away from the cylinder valve outlet when opening the cylinder valve.
Always secure the cylinder safely and never move with regulator and hoses connected. Always check for leaks.
Never deface or alter any cylinder
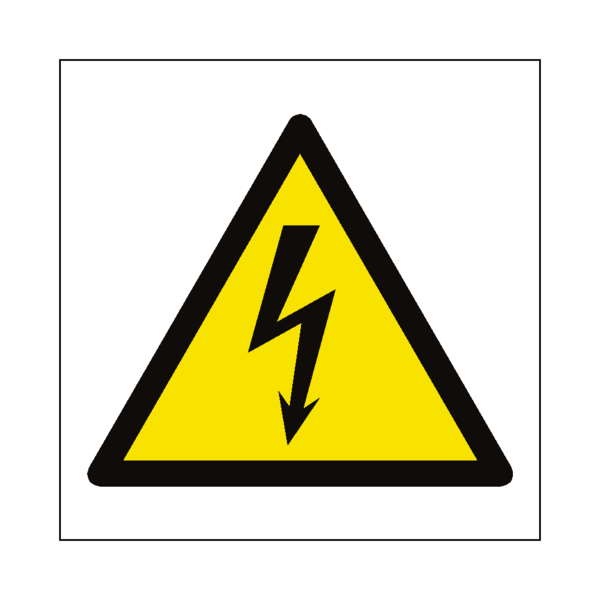
General electrical safety
The equipment should be installed by a qualified person and in accordance with current standards in operation. It is the users responsibility to ensure that the equipment is connected to a suitable power supply. Consult with your utility supplier if required.
Do not use the equipment with the covers removed.
Do not touch live electrical parts or parts which are electrically charged.
Turn off all equipment when not in use. In the case of abnormal behaviour of the equipment, the equipment should be checked by a suitably qualified service engineer.
If earth bonding of the work piece is required, bond it directly with a separate cable with a current carrying capacity capable of carrying the maximum capacity of the machine current. Cables (both primary supply and welding) should be regularly checked for damage and overheating. Never use worn, damaged, under sized or poorly jointed cables. Insulate yourself from work and earth using dry insulating mats or covers big enough to prevent any physical contact.
Never touch the electrode if you are in contact with the work piece return. Do not wrap cables over your body.
Ensure that you take additional safety precautions when you are welding in electrically hazardous conditions such as damp environments, wearing wet clothing and metal structures. Try to avoid welding in cramped or restricted positions.
Ensure that the equipment is well maintained. Repair or replace damaged or defective parts immediately. Carry out any regular maintenance in accordance with the manufacturers instructions.
The EMC classification of this product is class A in accordance with electromagnetic compatibility standards CISPR 11 and IEC 60974-10 and therefore the product is designed to be used in industrial environment only.
WARNING: This class A equipment is not intended for use in residential locations where the electrical power is provided by a public low-voltage supply system. In those locations it may be difficult to ensure the electromagnetic compatibility due to conducted and radiated disturbances.
Materials and their disposal
Welding equipment is manufactured with BSI published standards meeting CE requirements materials which do not contain any toxic or poisonous materials dangerous to the operator.
Do not dispose of the equipment with normal waste. The European Directive 2012/19/EU on Waste Electrical and Electronic Equipment states the electrical equipment that has reached its end of life must be collected separately and returned to an environmentally compatible recycling facility for disposal.
For more detailed information please refer to the HSE website www.hse.gov.uk
Eye protection
Welding arc rays from all the welding processes produce intense, visible and invisible (ultraviolet and infrared) rays that can burn eyes and skin.
Wear an approved welding helmet fitted with an appropriate shade of filter lens to protect your face and eyes when welding or watching.
Wear approved safety glasses with side shields under your helmet.
Never use broken or faulty welding helmets.
Always ensure there are adequate protective screens or barriers to protect others from flash, glare and sparks from the welding area.
Ensure that there are adequate warnings that welding or cutting is taking place
See the chart below that gives you an appropriate filter lens shade number based on the amps being used and the welding or cutting process.

Comments