What is 'Pulsed MIG' welding?
- Nov 7, 2018
- 3 min read
Pulsed MIG is an advanced form of welding that takes the best of all the other forms of transfer while minimizing or eliminating their disadvantages. Unlike short circuit, pulsed MIG does not create spatter or run the risk of cold lapping. The welding positions in pulsed MIG are not limited as they are with globular or spray and its wire use is definitely more efficient. By cooling off the spray arc process, pulsed MIG is able to expand its welding range and its lower heat input does not encounter the problems on thinner materials.
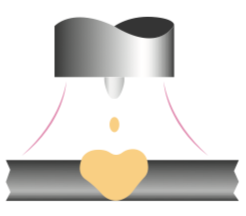
In basic terms, pulsed MIG is a transfer method where material is transferred between the electrode and the weld puddle in controlled droplet form. This is achieved by controlling the electrical output of the welding machine using the latest control technologies. The pulsed MIG process works by forming one droplet of molten metal at the end of the wire electrode per pulse. When ready the pulse of current is used to propel that one droplet across the arc and into the puddle.
Pulsed MIG welding has had quite an evolution since it was first introduced to the marketplace. In the 1980’s, the process was highly complex and was in general performed by the most skilled welders. The process was highly dependent on the operator skill and knowledge to know exactly how to set the machine parameters.

Today, the development of equipment utilising the latest technologies and programming removes many of the complexities. The machines often have pulse, double pulse modes, contain a large library of welding programs, automated setups and programming features.
As a result, the operator can set just a very few relevant parameters and the control will automatically adjust all the other parameters.
This is often referred to as “synergic” control. The synergic operation of the machine makes it easy to use even for relatively new and inexperienced welders. Its sophisticated control and monitoring electronics are “adaptive” to adjust for variations in conditions such as arc length, material gap etc.
Many of these state of the art power sources on the market today are those that provide pulsing capabilities. They are often presented to make welding easier for the operator and produce a high quality welding result with an excellent “cosmetic” finish.
What is often not understood is that these machines can also result in cost savings. Initial capital investment on the machine may be higher than conventional power sources but the advantages they present will often reduce the overall welding costs and provide a higher return on your investment in the long run.
Some of the key advantages include:
• Improved Productivity
Pulsed MIG offers high deposition rates. In addition, since the new machines are simpler and adaptive, it is easier to weld with pulsed MIG than other transfer methods, this results in less time spent training.
• Consumable Savings
The Pulsed MIG machines due to their control offer a wider operating range as they extend the low and high range of each wire diameter. Therefore, instead of using and stocking several different wire diameters to cover different applications for example 0.8, 1.0, 1.2mm one wire size 1.2mm can be used. This in turn results in better pricing for more volume purchases of the one size wire, one size consumables (Mig torch, tips, liners, etc.) and reduced changeover labour costs as there is no need to keep changing feed rolls and other consumables.
• Improved Weld Quality
All the advantages of Pulsed MIG process result in overall better quality of the finished weld. The more stable arc and spatter free welding, results in labour savings in weld finishing and additional clean up and grinding. The technology of these power sources also provide these high quality welds to be made by welders with relatively less training.
• Spatter and Fume Reduction
Compared to conventional MIG/MAG, Pulsing offers reduced spatter and fume. A reduction in weld spatter results in cost savings because more of the melted electrode wire is transferred to the weld joint and not as waste surface spatter on the product and surrounding work area. A reduction in the welding fumes creates a safer and healthier environment for the work area and workshop in general.
• Heat Reduction
Pulsing offers controlled heat input leading to less distortion and improved overall quality and appearance which means fewer production problems. This is especially important with stainless, nickel and other alloys that are sensitive to heat input.
• Energy Saving
The new technology inverter power source is very energy efficient and many have hibernating functions which provide energy on demand and can often cost less than a 60w light bulb to run in standby mode.
Comments